I have nothing against digital transformation imperatives or the millions of dollars and hours put toward it over the past decade. It was and remains an essential foundation of 21st-century value production. Picking up on a recent post, I will say that if anything the job is not done.
Productivity Recognition: Digital Transformation’s final frontier
As much as the rationale for digital transformation was as “essential foundation,” no organization should invest to lay down foundations without clear focus on the end. In other words, digital transformation’s only value is sustained and improved value production. For businesses, that means profitability; for government: effectiveness and efficiency. Both resolve to productivity.
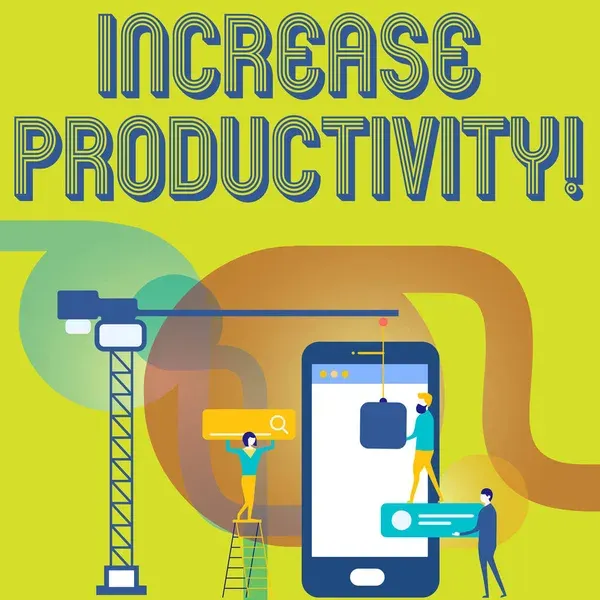
As the linked post suggested, especially in Canada, signs of digital transformation are everywhere except in productivity numbers. Why is that? Probably a lot of things, but high on the list has to be the organizations’ (and let’s be honest: executives’) mental models of what and how technology affects their organizations. Also, an inevitable form of “scope creep” probably has a dampening effect.
Whether the technology represents a sales channel (eCommerce), operational integration (eBusiness), automation, or otherwise, in a transformation there is necessarily a change to an existing, prevailing approach. That often got passed off as “analog,” as in replace analog methods with a digital alternative. But that anodyne description hides that the transformation is really about changing how (much) labour is used. It’s merely the labour:capital tension writ anew.
No doubt, McKinsey, Accenture, HBS/HBR, and others have labouriously constructed data-intense models, but I offer three relatively simple, broad-brush alternatives for how one might perceive technology impacting value production. (There are, of course, other perceptions but the focus is on value production, not conception or problem solving, etc.) The order is least to most troubling for labour and unions. That does not imply preference.
Technology enables a person to do their thing better, faster
Think about simple machines: levers, wheels, power tools… word processing and spreadsheets for office workers. In this case, technology always supports and requires a human actor. The human actor does less and less as the technology gets more sophisticated, to the point of now merely asking for specific help (i.e., “prompting” AI).
This type of transformation can have a direct productivity impact and requires no change to the system of measuring productivity. For a financial analyst doing statistics on a lot of data, Excel™ will do it much faster than with a calculator, which is in turn faster than the unaided option. The analyst ought to do more separate analyses in the same amount of time. That’s productivity. If the tool enables deeper analysis to be performed, the time on a given problem analysis may not change—though more is being done. That’s not going to reveal productivity increase.
If the technology doesn’t appear to affect the productivity numbers, gains may get lost in raised expectations and expanded workload. Looking for higher-level productivity while ignoring the deeper analysis cost will prove a fail for the organization in practical terms. Notably, it is not a failure of the technology to produce productivity gains.
Technology changes what a person does
The great fear propagated by labour unions about digital (and any other kind of technological) transformation is that the technology will eliminate work and jobs. (See next section.) Rather than leaning into this, organizational leaders recoiled to deny that anything like that would happen—at least not in an uncontrolled way. But for this kind of technological transformation to be effective, it necessarily has to change what people do.
Consider eCommerce, which is not so different from drive-through service. eCommerce is the replacement of a physical sales and delivery channel by one that is Web based. (Similarly, the drive-through replaces standing in line for takeout service with sitting in your car.) Obviously, the nature of people’s work is going to change somewhat despite the same basic business activity in play.
Whether in-store or online: a customer wants something; the customer shops and is shown the item; the customer can purchase the item; the item is given to the customer. Post-sales support is provided.
With eCommerce it’s done without face-to-face interaction, much of the human activity happening in the background—more like wholesale than traditional retail. The salesperson may (we eventually realized, often needs to) personally engage the customer by phone or via online chat. The item is stocked and pick/packed centrally at a warehouse not the stockroom or off the shelf. Entire ordering, inventory, distribution, and financing processes and dynamics change. This example is oversimplified, including structural labour inhibitors (e.g., a salesperson on the floor doesn’t translate well to a web environment). More frequently, technology is added to the operation without material change to what the person engaged with it does fundamentally.
For example: in a digital transformation the organization digitizes the internal expense claim process. Employees no longer assemble receipts and remit them with a written expense claim. They enter the information (digitally) into SAP or some other ERP.
- If claimants continue to remit the paper receipts for a clerk to marry to the systemic claim, what’s being saved? Surely, data entry is streamlined and becomes “one touch”, though the job of entering the information into the system moves from low-cost clerk to higher-cost claimant (usually executives, salespeople, and so forth) or another admin.
- If claimants input the claim with attached receipt scans directly into the system, the clerk now performs a quality check to ensure the receipt and entered amounts match. (The clerk may also assess acceptability.) That may be a little better and certainly changes what the clerk does to add value.
- If, however, an optical character reader (OCR) pulls the numbers off the scanned receipt and performs the correlation/matching function with an automated assessment, a clerk is no longer necessary. Perhaps that person becomes an adjudicator to review those claims deemed questionable by the automation. That person would cost more because s/he is adding more value. More importantly, with the automation s/he would likely perform considerably more work (i.e., more claims) at a higher quality in the same time.
- If, finally, that system did not require the claimant to do anything more than input digital (scanned) versions of the receipts for the automation to process, the higher-cost time of the claimant would also be recaptured. That time would, presumably be used by that person to increase added value (i.e., it removes waste).
That’s the transformation of work and the “business.” The hazard is that it definitely requires individuals to do different things and/or to focus on higher-value work. It demands reimagination of roles and change management to shift employees’ understanding of how they add value and where their work is most productive. It also means that the metrics and measure by which productivity is targeted and monitored must change. It should be obvious how each scenario of the simple example has far-reaching impacts on not only how labour does its job but how management addresses, focuses, and monitors its operation.
Technology replaces a person
This is automation, pure and simple: self-controlled vending machines and robots. Ot is, of course, the most radical change to the labour construct. Labour for a particular function is eliminated as broadlooms replaced weavers. Door scanners and badges may effectively replace security guards. Organizations would like for online ordering and chat bots to replace humans; but they don’t. Not entirely. (And a security guard or two is still necessary.) It’s probably still a win, reducing the labour cost materially.
It seems there have been relatively few instances of outright replacement of people by automation recently. Much of that happened with mechanization, like factory robotics, and so forth. Maybe it has and will happen where:
- People are the last choice to perform the work. Say, pipeline flow monitoring, where SCADA devices do a much better job (and complain less about work conditions).
- The function is in the computer’s wheelhouse: finding, sorting, comparing, applying rules to enormous quantities of data… in other words, where an algorithm can do the job. Stock trading, travel booking, search-engine optimization, and so forth are examples.
- Judgment and interpersonal relationships are not critical. Even though a chat-bot can intercept and field common service enquiries, such as package tracking, for anything substantial (value producing, generally) or requiring delicate judgment, the human is harder to eliminate.
What generally happens in all of these instances—and happened with mechanized automation—is that humans become the technology’s supervisor. The technology does the work while the human ensures it is working. With mechanized equipment, that typically would mean oiled, not jammed, running the proper instruction set, and outputting the expected result. That holds true today and will probably hold true with Artificial Intelligence (AI) implementations. In fact, as automation gets closer to critical value production, the more important for it to be supervised.
Artificial Intelligence: not even artificial productivity
Productivity by replacing human labour is, of course, the big desire and deep concern about AI. Proponents and those business/government executives (and politicians) hoping for productivity leaps point to AI as a panacea. (Spoiler alert: It won’t be. For reasons that track to what’s provided above.) Where it works, it’s an obvious productivity gain because (some) labour is completely removed from the cost equation going forward, replaced by a one-time capital investment and much smaller operating costs (power, etc.). And, if the technology replacing the person is faster, so much the better.
Conclusion
None of this is an excuse or blame for the shortcoming of proven productivity gains manifesting from digital transformation. First, a transformation is a journey not an event, and the next stage of the journey in digital transformation is to begin the process of finding and squeezing out increased productivity. Second, to achieve that will likely not happen by replacing labour (which only shifts productivity from labour to capital anyway) but by changing what labour does to produce the firm’s value working with the new digital technologies and structures.[1] Third, and importantly, productivity increases easily disappear if one loses focus and “deepens” work without recognition.
Now is the time to do the hard work of changing the nature of digital labour:capital integration to reflect the organization’s value production today (i.e., in a digital environment). That is where real productivity gains will be found. But be very aware that productivity may disappear (doing more because more can be done) or not even happen (because people continue doing things that digitization was meant to eliminate) without ruthless focus on the end purpose.
Institute X is a transformation leadership consultancy and leader coaching firm. One of its online presences is The Change Playbook. Check out the abundance of pragmatic guidance for making change happen. Subscribe to be notified of new, fresh content. Contact us so we can help you in your specific circumstances.
[1] There will undoubtedly be shifts to the labour:capital ratios.